L'institut français du textile et de l'habillement vient d'implanter dans son bâtiment une plate-forme de développement ouverte aux PME qui veulent développer des textiles innovants à forte valeur ajoutée.
De mieux en mieux perçus et acceptés par les professionnels, les vêtements de protection vont encore gagner en confort et en fonctionnalités. Et l’Institut français du textile et de l’habillement (IFTH) compte bien y contribuer. L’organisme vient d’ouvrir une plate-forme de développement avec Techtera, pôle de compétitivité consacré aux matériaux souples et aux textiles techniques. Réunissant cinq nouvelles technologies, leur plate-forme, baptisée Mistrak est ouverte aux PME qui souhaitent développer des textiles innovants et à forte valeur ajoutée.
Avec le Sportwear, le secteur des EPI (Equipements de protection individuelle) compte parmi les plus actifs avec des développement impulsés par les utilisateurs. « Les plus fortes demandes concernent la protection chimique, l’amiante, les produits phytosanitaires et les virus mais aussi la protection multirisques pour se protéger contre la flamme, les produits chimiques, etc », constate Carole Garbowski, chef de produit EPI à l’IFTH. Cette spécialiste relève aussi, parmi les plus fortes tendances, l’influence du sportwear dans la coupe et le design des vêtements professionnels. En résultent également ces membranes imper-respirantes et ces traitements déperlants qui évitent la pénétration des gouttes d’eau, des produits chimiques ou de tout autre substance. « Les industriels veulent aller un cran plus loin afin d’améliorer l’effet barrière, tout en laissant passer la respiration et en misant sur de nouveaux traitements de surface et de nouvelles fibres », rapporte la chef de produit de l’IFTH.
La toute nouvelle plate-forme de développement Mistral va y contribuer. Cet outil collaboratif implanté à Ecully, près de Lyon (69) dans les locaux de l’Institut, comporte deux volets. Le premier porte sur la mise à disposition d’outils de prototypage et le second concerne l’accompagnement individuel ou collectif des industriels. Plus de trois millions d’euros ont été investis dans cette plateforme collaborative qui occupe une surface de 800 m2. Afin de préserver le secret de fabrication des entreprises utilisatrices, quatre ateliers sécurisés y ont été créés. « Trois d’entre eux disposent d’une ligne complète dédiée au traitement et à la fonctionnalisation des structures textiles », explique de son côté Isabelle Ferreira, responsable de l’unité Textile fonctionnel à l’IFTH.
Les PME peuvent y tester, comparer, voir éventuellement additionner différentes technologies d’activation de surface et en évaluer le coût de production. Ces trois lignes pilotes comprennent plusieurs modules. A commencer par le fluor gazeux qui est employé pour nettoyer la surface d’un textile de manière à en augmenter la mouillabilité. A cette technologie est associée un autre module, à savoir le Rotor Spray qui consiste à déposer par jets contrôlés des réactifs chimiques, comme par exemple des résines anti-bactériennes ou déperlantes. Ensuite, le textile peut être passé dans un plasma afin de modifier sa surface sans en amoindrir la souplesse et le toucher. En amont et en aval de ces trois technologies, sont positionnés deux installations infrarouge. La première située en amont sert à pré-sécher la matière et augmenter l’efficacité de chaque traitement. La seconde située en aval, optimise la polymérisation des précurseurs appliqués à l’aide soit du Rotor Spray soit du plasma.
En fonction du cahier des charges de l’industriel, cette installation permet de confectionner, par exemple, des textiles multirisques anti-feu et antiseptique, d’augmenter leur déperlance et leur mouillabilité ou encore leur conférer des propriétés pour prévenir le risque chimique ou microbiologique.
D’autres modules sont également disponibles. Parmi lesquels la métallisation des supports par couches minces grâce à un procédé plasma. En clair, on envoie un gaz activé sur une cible métallique. Ce qui a pour effet d’en arracher les atomes qui viennent alors se déposer à la surface du textile. Ce procédé de métallisation améliore le confort et la respirabilité d’un tissu anti-feu. Ce même procédé peut être utilisé pour protéger les salariés contre la chaleur radiante, les ondes électromagnétiques ou encore pour fabriquer des textiles antistatiques afin de travailler en zone Atex (atmosphère explosive).
Enfin, dernier module, le Nanospining vise à la réalisation de filage de nanofibres. L’idée est de confectionner des membranes nanofibrées employées à la réalisation de vêtements ou de masque pour se protéger notamment contre différents facteurs extérieurs, tels que des virus ou des bactéries en milieu hospitalier par exemple. Des produits qui ont de l’avenir !
Eliane Kan
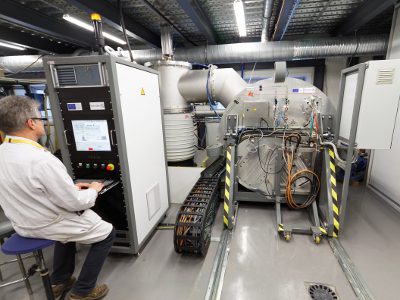
Commentez